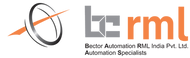
General & Preventive Maintenance
1.Maintenance Cautionary Notes
1.1 Important Precautions.
​
READ this manual before operating or servicing this equipment.
​
-
ALWAYS remove power and wait at least 30 seconds before connecting / disconnecting any internal harnesses. Failure to observe these precautions may result in damage to, or destruction of the equipment.
-
ALWAYS take proper precautions when handling static sensitive devices.
-
SAVE this manual for future reference.
-
DO NOT allow untrained personnel to operate, clean, inspect, maintain, service or tamper with this equipment.
-
DO NOT connect or disconnect any digital or analogue components to the equipment with power connected or damage may result.
-
Do not use any chemicals to clean this equipment, unless otherwise stated in this manual.
-
When using compressed air to blow down this equipment, do not direct the air stream at electric/pneumatic or other sensitive devices. Ensure correct PPE is used appropriately.
-
Do not wet wash any of the equipment unless stated to do so.
-
Report all defects immediately to your supervisor or manager.
-
When first installed all surfaces must be cleaned of all foreign material.
Ensure all energy sources are isolated before attempting to clean this machinery. All loose products should be gently brushed off the machine components with a small hand brush. If a vacuum system is installed for cleaning purposes use a small application head to remove loose product from this equipment.
Where applicable, follow the manufactures instructions stated in the original equipment manual. All safety warnings and cautionary advice must be observed.
Cleaning should occur at the end of each day’s production or before maintenance work. Cleaning of every station and work area on the process and line equipment is very important.
Clean with a dry lint free cloth or soft brush; use a vacuum attachment if installed.
Include cleaning for these areas:
​
-
All access points including guards.
-
All the floor area underneath and around the machine.
-
Sensors and switches.
-
Motors and gearbox units.
-
Pneumatic cylinders and fittings.
-
Internal and external surfaces and the dust extraction ducting including flexible tubing.
-
All product contact surfaces must be cleaned to an acceptable hygiene level.
If the product has been exposed to moisture and solidified a scraper with a hard plastic blade can be used. Under no circumstances is a metal blade scraper to be used. Once the hardened product has been removed the scraper and the cleaned area must be wiped down. Any wet areas after washing must be cleaned using a clean dry cloth. Wipe all areas afterwards using a clean dry cloth.
​
1.2 Personnel.
-
Only qualified personnel are permitted to operate, adjust, service or maintain `BRML' equipment.
-
Personnel are prohibited from interfering with machinery in any way when it is in operation.
1.3 Safety.
WARNING
Safety screens and covers must be maintained where fitted and replaced in the correct position after maintenance or servicing is completed.
​
1.4 Service, Repair & Adjustments
-
Before servicing or repairing, stop the machine and disconnect all energy sources.
-
Maintenance and adjustments must be performed with all energy sources isolated unless otherwise specified in this manual.
-
To isolate the machinery, refer to the “warning” page in this manual.
1.5. Pneumatic Supply
-
High pressure pneumatic systems are dangerous.
-
Do not service or troubleshoot systems with the compressed air supply on. Be sure to bleed off any trapped compressed air before working on components since it is possible to have high pressures trapped in the pneumatic or gas lines.

2.Maintenance Specifications
2.1 Pneumatic Cylinder Torques
For further information please refer to the OEM or the manufacturer.
2.2 Pneumatic System Settings.
Pneumatic Pressure – Regulator.
​

3. Maintenance Schedule
3.1 Magazine Maintenance Schedule

3.2 Plucker Maintenance Schedule
3.2.1 Bearings, Bushes and Cam Tracks.

3.2.2. Motors, Gearboxes, & Brakes.

3.2.3 Belts and Pulleys/Chains and Sprockets.
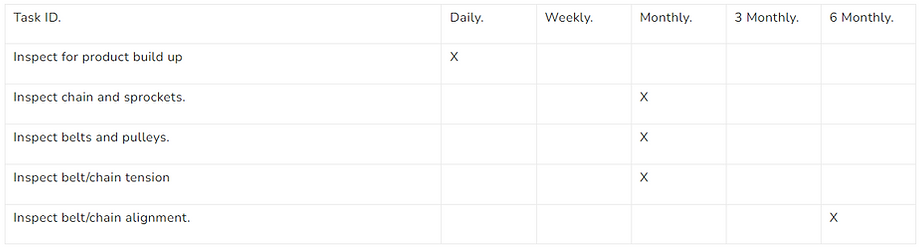
3.2.4 Pneumatic and Vacuum System
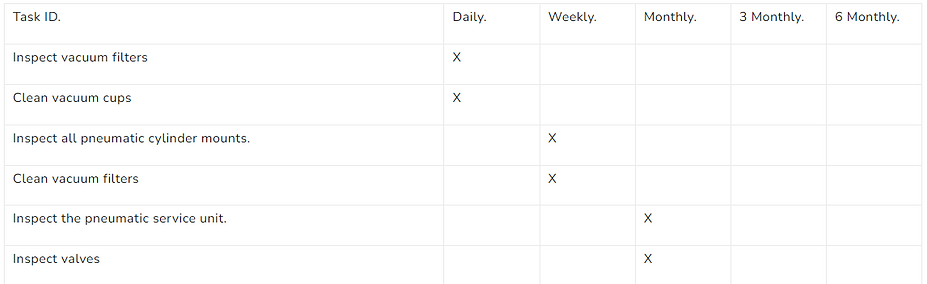

3.2.5 Chassis and Fasteners

3.3 Main Drive Maintenance Schedule
3.3.1 Bearings, Bushes and Cam Tracks.

3.3.2. Motors, Gearboxes, & Brakes.

3.3.3. Belts and Pulleys/Chains and Sprockets.
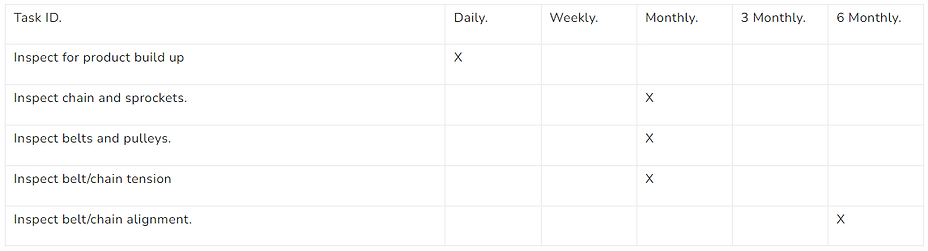
3.3.4 Chassis and Fasteners

3.4. Enclosure Maintenace Schedule.

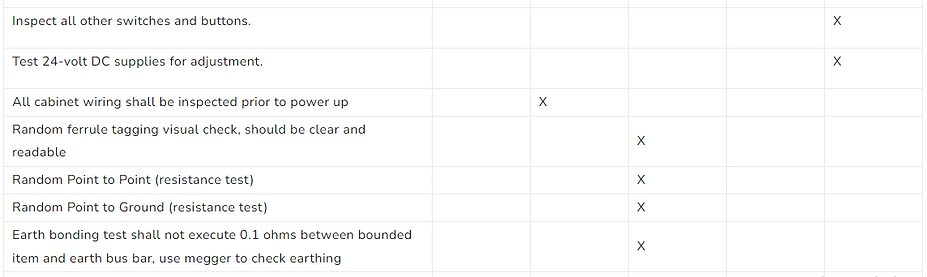

3.5. Chassis Maintenance Schedule.

3.6 Outfeed Conveyor Maintenace Schedule
3.6.1 Bearings, Bushes and Cam Tracks.

3.6.2. Motors, Gearboxes, & Brakes.

3.6.3. Belts and Pulleys/Chains and Sprockets.
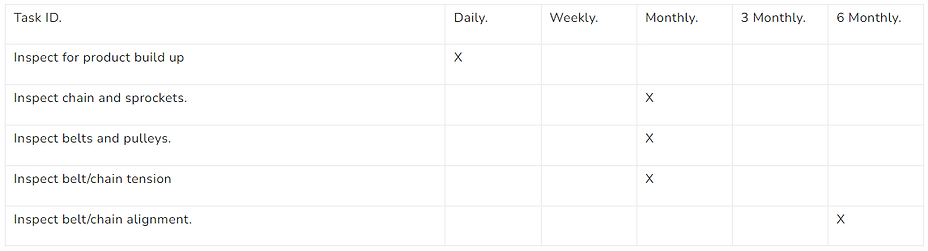
4. Maintenance Procedures
4.1. Bushes and Cam tracks.

4.2. Pneumatic Service Units.


4.3 Belts and Pulleys/Chains and Sprockets.


4.4 Drive Belt Tension.


Fig 1
4.5 Chain Tension.


4.6 Pneumatic Cylinders.

4.7 Pneumatic Cylinder Mounts.
Inspect the clevis pins, trunnions and rod ends for excessive wear – report all defects to your supervisor.
4.8 Chassis and Fasteners.

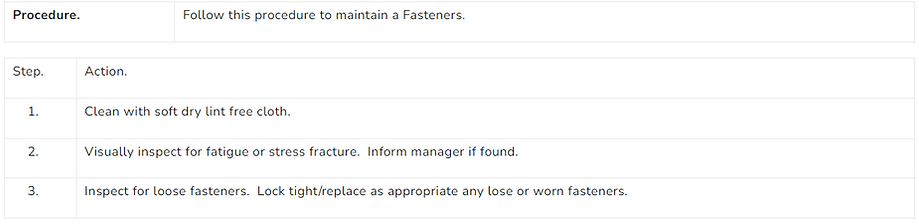
4.9 Photo Electric Sensors.
Note: Click on the Image for the Manual

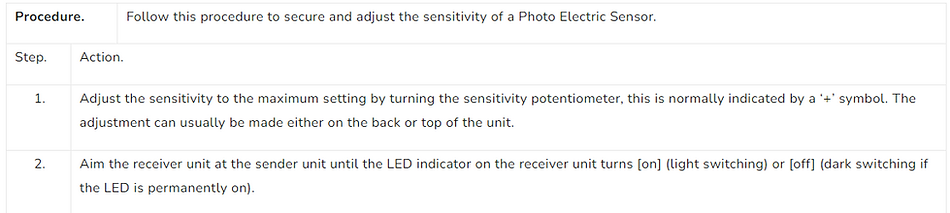

4.10 Pneumatic Energy System.


4.11 PLC Battery Check.

4.12 Fan Filter.

Inspect the fan filter in MCC cabinet every month.
4.13 Vacuum Filters and Valves.

4.14 Vacuum Cups


4.15 Pneumatic Service Units.



For default pneumatic settings, please refer to “Maintenance Specification” in section 4.2.
5. Lubrication System
lubrication system is a critical component of any machinery that relies on the movement of mechanical parts. The purpose of a lubrication system is to provide lubrication or oil to the various moving parts of a gears or machinery to reduce friction and wear and tear, prevent overheating, and increase the lifespan of the machinery.
Please refer the below Lubrication Schedule
5.1 Chains


5.2 Bearings
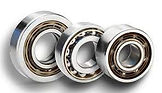




5.3 Gear Motor / Gearbox
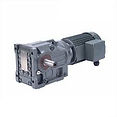


6. Maintenance Drawing
Click on the below Assemblies for the Maintenance Drawings