
Troubleshooting
1. Overview
If a mechanical fault has occurred then the machine will have to be shut down and inspected for the probable cause (e.g., loose belt or chain, broken component, loss of air pressure, etc.)
1.1 Mechanical Parts Trouble shooting
The filled Cartons are entering the Outfeed Conveyor and the Capacitive sensor detect the products inside the Carton. The Cartons are rejected which not have the products and the cartons are moved out.
Faults
Trouble Symptoms
Probable Causes
Tests & the Remedy
Induction Motors
Fail to start without load.
MCB Trips
(Automatic switch trips off, slow start with electro-magnetic noise)
1.Short circuit of circuit switches
2.Incorrect wiring
3.Poor contact at terminals
4.Windings grounded & Broken winding
1.Check circuit switches and replace.
2.Check wiring according to nameplate or refer electrical drawing.
3.Lock tightly
4.Factory Repair
Loading after start
MCB Trip (Fail to restart due to trip-off of automatic switch)
1.Insufficient capacity of fuse
2.High load at low voltage
1.Replace fuse if wiring permits.
2.Check circuit capacity and reduce load
Motor overheats
1.Motor Overloaded or intermittent overload.
2.Motor improperly connected to the Circuit
3.Electric Shock
4.A lack of ventilation
If there is something blocking the ventilation holes for your electric motor, then hot air won’t escape.
1.Remove the Load, run motor Idle. Give it General Inspection. Apply Load Gradually & note characteristics. Inspect for Localized heating.
2.Check Motor Line Connections
3.Check the Earthing of the Motor.
4.Scheduling regular maintenance on your motor can help reduce this risk.
Bearing Overheats
1.High Belt tension.
2.misalignment between motor & machine shaft
3.High Bearing noise
1.Adjust Belt tension.
2.Re-align.
3.Replace the damage bearing
Noise
Electro-magnetic noise induced by electricity.
1.Occurrence from its first operation
2.Sudden sharp noise & smoky
1.coulb be normal.
2.short circuit of windings, Factory repair
Mechanical noise caused by machinery.
1.Loose belt sheave
2.Loose coupling
3.Rubbing as a result of ingression of foreign materials
4.Wind noise
5.Bearing abrasion or they lack lubricating oil.
6.The rollers are misaligned
1.Adjust key and lock the screw.
2.Adjust the position of couplings, lock key and screw.
3.Clean motor interior and ventilation ducts
4.Noise induced by air flowing through ventilation ducts.
5. Have the Induction motor serviced:
(i) Change or clean the bearings.
(ii) Change or add the lubricating oil.
6.Realign the rollers
Vibration
Electro-magnetic vibration
1.Short circuit of windings
2.Open circuit of rotor
Factory repair
Mechanical vibration
1.Unbalanced rotor & Unbalanced fan
2.Unsymmetrical centers between belt sheaves
3.Rollers Central points of couplings do not lie on the same level.
4.Improper mounting installation
1.Factory repair.
2.Align central points
3.Adjust the rollers central points of couplings to the same level.
4.Lock the mounting screws
Pneumatic System
Actuator Moving Abnormally Slow
Excessive air choke
1.Flow control valve incorrectly adjusted.
2.Plugged air silencer.
3.Air leak or squeezed tube
4.Plugged filter
5.Damaged cylinder or seal
1.Readjust the valve.
2.Replace or clean silencer.
3.Repair air leak or tube.
4.Replace air filter.
5.Replace cylinder or seal.
Pressure too low
1.Damaged or incorrectly adjusted pressure regulator valve
2.Plugged filter
3.System leaks
4.Directional or other valve open due to dirt or failed pilot circuit.
5.Cylinder pipe, piston or seal damaged
1.Replace regulator or readjust rating as shown in drawing.
2.Replace filter.
3.Fix leaks.
4.Locate damaged part and clean or replace it.
5.Repair or renew damaged parts.
Filter / Regulator / Lubrication Unit
Air leak at regulator
1.Continuous air leak from the small vent hole in the regulator bonnet
2.Failure of the diaphragm
1.The regulator should be scheduled for repair. Overhaul kits with diaphragm and seals are available for most standard regulators.
2.Replace a diaphragm or the seals as soon as possible after the leak is discovered.
Pressure problems
If diaphragm is cracked or broken
A high velocity air leak at the vent hole will occur. Replace diaphragm.
Filter problems
Over-contaminated, the filter element will create a pressure drop which may affect system operation
Clean or replace the filter element regularly
Directional Control Valve Not Changing Position
Coil not picking up.
Electric failure
Clean or replace the filter element regularly
Valve spool stuck
1.Impurities between spool and sleeve
2.valve pilot not working
1.Replace valve.
2.Replace or clean piloting part.
Proportional valve not responding.
1.Valve not receiving set value from program.
2.Set value received but valve not responding
1.Locate and fix electric failure.
2.Replace the proportional valve.
Air Cylinders
No movement
1.Pressure too low
2.Piston seal leak
3.Scored cylinder bore
1.Check pressure at cylinder to make sure it meets circuit requirements.
2.Operate valve to cycle cylinder.
-Observe fluid flow at valve exhaust ports at end of cylinder stroke.
-Replace piston seals if flow is excessive
3.Replace necessary parts.
-Eliminate contaminants from air supply.
Erratic movement
1.Load misalignment
2.Large difference between static and dynamic friction
1. Re-align cylinder and load.
2.Install flow control valves to provide back pressure to control stroke.
Cylinder body seal leak
1.Loose tie rod
2.Seal deterioration - soft, gummy
3.Seal deterioration - hard, brittle. Usually due to temperature extremes.
Repair or replace.
Rod gland seal leak
1.Torn or worn seal
2.Seal deterioration - hard, brittle. Usually due to temperature extremes.
1.Examine piston rod for dents, gouges or score marks. Repair or replace.
-Check gland bearing for wear. Repair or replace.
2.Replace seals and shield cylinder from temperature extremes.
Gearbox
Overheats
Gear case becomes unusually hot.
1.Overload
2.Insufficient or excessive lubricating oil
3.Contaminated oil
4.Oil viscosity is improper
5.Bearing are improperly mounted
6.Shaft is connected improperly
7.Air vent port is closed
8.Ambient temperature is too high
1.Decrease load or use a larger model.
2.Adjust oil level so it aligns with mark on oil gauge
3.Flush interior and replace oil.
4.Change oil with one having the proper viscosity.
5.Reassemble and tighten properly
6.Align properly
7.Remove rubber plug from oil cap
8.Install cooling fan or move to cooler area
Noise
Unusual or excessive noise
1.Improper meshing
2.Bearings are damaged or worn
3.Overloaded
4. Insufficient oil
5.Oil seal is not wet with oil
6.Bearing are improperly mounted
1.Adjust properly
2.Replace bearings
3.Decrease load or use a larger model
4.Add oil so level aligns with oil gauge
5.Lubricate
6.Adjust the bearing
Vibration
Vibration is excessive
1.Gear teeth are worn.
2.Bearings are worn or damaged
3.Mounting bolts are loose
1.Replace wheel
2.Replace bearings
3.Tighten
Vibration
Oil Leaks
Oil Leaks
1.Oil seal is defective.
2.Cover mounting bolts are loose
3.Air does not escape
4.Excessive oil
1.Replace oil seal
2.Tighten bolts
3.Check oil cap.
4.Adjust oil level so it aligns with mark on oil gauge.
2.Equipment's Alarms Troubleshooting
Overview: -
​
Should a program or operational fault occur please refer to digital screen of PLC in main control panel. In most cases the screen will detail the cause of the fault.
If a mechanical fault has occurred then the machine will have to be shut down and inspected for the probable cause (e.g. loose belt or chain, broken component, loss of air pressure, etc.)
There are details that can be referenced that specify all the types of alarms associated with a device and actions to solve each fault.
1.Normal Screen

Type of Faults
Possible Cause
Solutions
Machine not running or Input / Output not getting
-
PLC may be in STOP mode
-
Wire may be loose of I/O device may be damage
-
Set the PLC in RUN mode
-
Check the I/O device and see the signal is getting to PLC with the help of PLC Screen
2.Safety Fault

Type of Faults
Possible Cause
Solutions
Red indication lamp glows continuous and machine not resetting
-
E-Stop on control panel operated
-
Guard door open
-
Release E-stop if operated
-
Close the Guard door
-
Press the Stop/Reset button
3.Main Drive Motor Fault
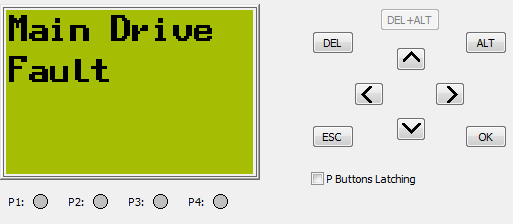
Type of Faults
Possible Cause
Solutions
Main drive motor not running
-
Motor running feedback not getting to PLC
-
Motor is jam because of mechanical problem
-
Check the feedback of motor
-
Solve mechanical problem